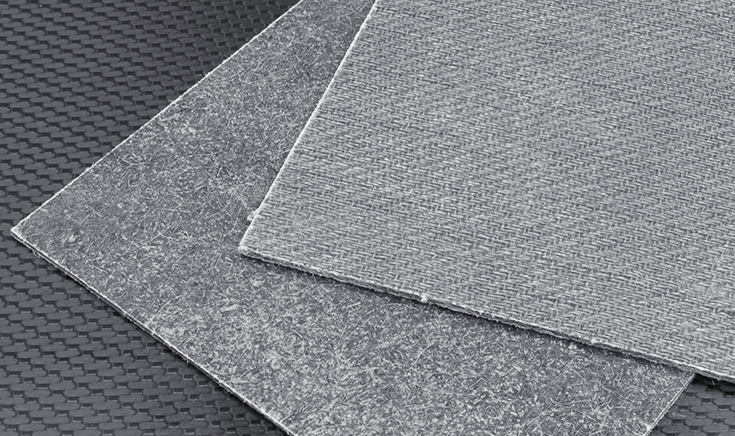
06 Nov Automobile: the race to reduce weight also involves biocomposites
Article published in the ValBioMag, 28.10.19
Our cars could become biosourced. And not only in terms of their fuel!
If we replaced the materials that make up the car with biosourced alternatives, what impact would this have on the environment?
The cost of lightering: the main obstacle
To climate emergency, there is an urgent need to increase the energy efficiency of conventional and electric vehicles. To date, weight reduction initiatives have resulted in several innovative solutions based on steel, aluminum and composites, and the great complexity of this optimization makes weight reduction one of the most challenging tasks for modern automotive designers and engineers. Overall, the cost of weight reduction has been identified as the main obstacle to the use of lightweight materials in the mass production of vehicles, and natural fibre-reinforced composites have a major role to play as an alternative to traditional plastics. Today, on a city car there are between 150 and 200 kg of plastics, or about 20% by weight of its composition. In the future, up to 90% of this plastic could contain biosourced, entirely or partially. Among the biosourced materials that make up the car, an average of 90% of natural organic materials (natural fibres, textiles and leathers) and 10% of biopolymers (PLA, PE…) are found. Most of the plastic used comes from recycled polymers, although it is petroleum-based.
Various biomasses can be used in a wide variety of applications, such as Ford :
- Castor oil: nylon fuel lines and soft-touch foam in dashboards;
- soy-based polyurethane foam: seat backs, cushions and headrests;
- rice shell: reinforced plastic in electric harnesses;
- coconut shell fiber: reinforced plastic trunk lining.
- Cellulose-reinforced plastic: replacement of fibreglass in armrests and consoles;
- wheat straw: reinforced plastic in storage bins; Kenaf: moulded plastic door part;
Manufacturers come together
The ALLIANCE project brings together six European car manufacturers (DAIMLER, VW, TME, CRF, VOLVO and OPEL), four suppliers and eight research partners who have joined forces to face the high cost of innovations in car weight reduction. The main objectives of the ALLIANCE project are to reduce energy consumption by 10% and the impact on global warming by 6% compared to a conventional vehicle, and the project results show that transferring ALLIANCE technologies to a complete vehicle in our daily lives would result in a 15.6% reduction in the weight of an internal combustion engine vehicle, or a reduction in global warming potential by 6 to 8%, most of which can be achieved at a cost of €3 per kg saved.
A research project on the theme: COMPOSENS
The Interreg COMPOSENS project aims to develop cross-border polymer-wood composite materials or high-performance vegetable fibres with a low environmental impact for the production of light and recyclable biocomposites, using renewable resources from the Franco-Belgian region: wood and natural fibres, such as hemp and flax. These fibres make it possible to produce biocomposites lighter than composite materials incorporating glass fibres for applications in the automotive sector in particular.
7 partners: Certech (lead partner), CRITT M.D.T.S., IMT Lille Douai, ARMINES, Institut National de la Recherche Agronomique (INRA), ULg and ValBiom
Duration of the project: 1 April 2016 – 30 September 2020